In this presentation, Gary Klein shares important information about air source heat pump water heaters (HPWH), with particular attention paid to where the warm air comes ...
A Different Way to Pipe
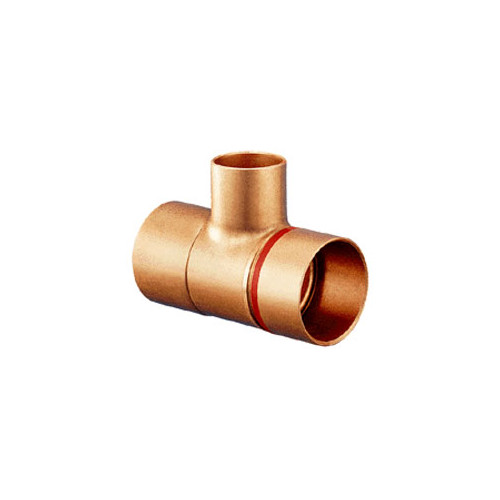
I was raised by Bell & Gossett and gobbled up the writings of the late, great Gil Carlson for a lot of years.
I learned about Monoflo systems and primary-secondary pumping, the importance of the point of no pressure and system balance and early radiant heating systems with copper pipes. I learned that we call centrifugal pumps “circulators” when they’re in closed systems because that’s exactly what they do, and that they often wind up on the return side of the boiler because that’s where the water is coolest. I learned how important this was years ago when mechanical seals couldn’t take very high temperatures, and that all of this was happening at a time when the hot water industry was tinkering with high-temperature systems. This, to compete with steam.
I learned a lot of tradition from the rep, and a lot of hydronic history. I learned how to think like an American heating guy.
I was in Germany talking to an engineer once. The subject of Monoflo tees came up and I was pretty proud of what I knew. He had never seen such tees with their tight internal cones and I was explaining how we do things in America. The man listened and then got furious. He said that we were designing fixed and permanent pressure drops into our American systems and that meant that we had to use larger-than-required circulators. We were wasting the world’s electricity. I tried to explain that this was how the early hydronics industry competed with the one-pipe-steam folks, but he told me that we were irresponsible. He really was furious. It was a heck of a way to start a relationship.
I showed him primary-secondary pumping and he shook his head and showed me these big tanks with many tappings that they use in European boiler rooms. These tanks act as wide spaces in the piping road, places where the circulators can hydraulically disconnect from each other. The principle is the same one that makes primary-secondary pumping work, but he was convinced that their way was better. It got pretty parochial at that point. I just listened and tried my best to learn.
There was this house in the suburbs of Frankfurt. The heating contractor had placed a boiler and an indirect water heater in the basement. The boiler sat on top of the tank. He used two factory-fabricated units that encompassed the circulator, valving, gauges, thermometers, three-way valves, differential-pressure regulators and whatnot. These were mounted on a wall near the boiler. One was for the high-temperature circuits and the other was for the radiant. He piped from these units to manifolds upstairs. Some of these manifolds served the PEX tubing that ran beneath the floors of the radiantly heated areas while others served panel radiators.
I like this concept. Each panel radiator connected to the manifold with supply and return lines that were tiny by American standards. Water flowed continuously between the boiler and the manifolds. The boiler had are set control to monitor the outdoor weather temperature and change the supply water temperature to the manifolds.
Each panel radiator had a thermostatic radiator valve that the occupants could set to their comfort needs. The water that flowed to the manifolds would move (or not move) through the panel radiators as the TRVs modulated. The differential-pressure regulators in the near-boiler piping pretty much nailed the circulators on their performance curves.
This was a wonderful mix of constant flow with variable temperature (on the boiler side of the manifold) and variable flow with variable temperature (on the radiator side of the manifold), and it was so simply done. The system was fine-tuned to both the outdoor and indoor conditions and this is pretty standard piping in Europe. I think we can learn from their use of manifolds. We use them in America for radiant, sure, but I think manifolds are well worth a closer look when it comes to radiators, especially if we start to use more panel radiators.
Panel radiators feel good.
The engineer got angry with me because I was looking at his panel radiators and asking how the water flowed into them. They were set up on a one-pipe system. I couldn’t see how the water made it from the pipe into the radiator. That’s when I asked if they had some sort of Monoflo tee going on inside the pipes. I made my sketch.
He told me that the water flowed into the panel radiators because the pressure drop across the pipe was greater than it was through the panel radiator. The tees were spaced widely – the width of the panel radiator. Oh.
Gil Carlson used to say, “When two piping circuits are interconnected, flow in one will cause flow in the other, to a degree depending upon the pressure drop in the piping common to both.” That’s the basis of the Monoflo tee, and also of primary-secondary pumping.
The engineer in Germany drew Deta-P on a piece of paper for me and shook his head. “Irresponsible,” he said.
I have much to learn. Working on it every day, though!
Leave a comment
Related Posts
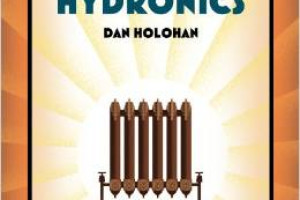
In this all-technical three-hour seminar, Dan Holohan will give you a Liberal Arts education in those Classic Hydronics systems. He’ll have you seeing inside the pipes as...
We always have turkey for Thanksgiving. I mean who doesn’t? My job wasn’t to cook it, though; it was to eat it.