This all-technical, three-hour seminar will make you familiar with the many types of old steam heating systems and what goes wrong with them. Dan Holohan’s easy-to-follow...
Four Things To Look Out For in Steam-Boiler Pressure Controls
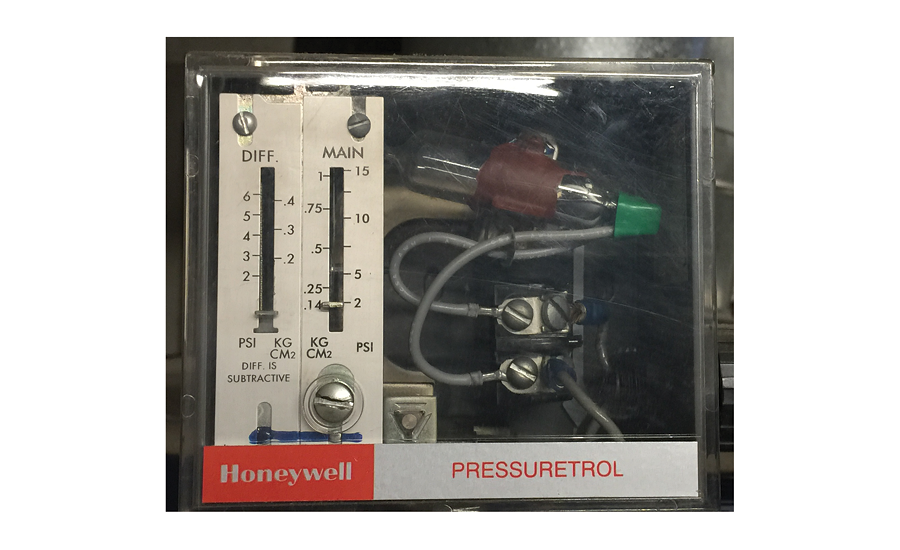
"Something is wrong with the boiler control. I have to keep pushing the reset button,” the frantic school custodian said when I answered the phone one cold January morning.
“Which control is it?” I asked.
“The one on the boiler,” he replied. “Please hurry!”
When I arrived at the chilly school, the custodian pointed to the limit pressure control and I saw it was set for 12 psi. The boiler pressure gauge read 12 psi. The boiler operating pressure control was set for 15 psi. Steam was spewing from the boiler feed vent like an old locomotive. I adjusted the operating pressure control to the normal steam pressure. Within a short time, the boiler operated the way it was supposed to and the building had heat. I asked who changed the control settings since we were there last and he shrugged his shoulders.
When visiting a steam boiler room, I like to note the steam pressure settings on the pressure controls. I see settings ranging from 2 to 14 lb. People get confused about the proper setting of a steam boiler pressure control, especially on a boiler with a multi-position burner. Typically, the steam pressure inside a commercial boiler is controlled by two main pressure controls; one is the operating control and the other is the manual reset limit control.
Operating pressure control
The boiler operating control is set at the desired steam pressure of the boiler. On-off steam systems for comfort heating are usually set for an average of 2 lb. of steam pressure. The operating control is an automatic one that will cycle the boiler between the settings of the pressure control as long as there is a call for heat. For example, you could set the control for 3 psig with a 2-lb. differential. The boiler will cycle between 1 and 3 lb. of pressure.
If the boiler uses a firing rate or modulating control, that changes the strategy a bit. I would set the operating control slightly higher, to operate between 2 and 4 psi and the firing rate or modulating control to operate between 1 and 3 psi. If the boiler steam pressure reaches 3 psi, the burner will drop to low fire and stay there until the boiler pressure drops. If the pressure drops to 1 psi, the burner will drive to high fire until it reaches 3 psi.
- Can it be higher? Many customers and contractors will bristle when I ask them to try setting the boiler to 2 psi. I tell them the iconic Empire State Building in New York is 102-stories tall, 1,250-ft. high and heats the building comfortably with about 2 to 3 psi. I contend if a building that size can be heated with 2 to 3 psi, then their building should be able to do the same. If they cannot heat the building at that pressure, most likely system issues require attention. I have found some buildings require higher steam pressures because the system has steam to water heat exchangers that require higher steam pressures.
- How high is too high? When the steam pressures are higher than 5 psi, system problems start to occur. If you have a boiler set at 7 psi, the steam temperature is about 232° F. Steam traps will open once the steam temperature drops 10° to 20°. The discharge temperature of the trap will be between 212° and 222° into a pipe at atmospheric pressure. At those temperatures, the water flashes to steam. The flash steam will slow the operation of the system because steam is on both sides of the trap.
Another consideration is the flash steam will find its way to the boiler feed unit and escape through the vent. This means we have to bring in fresh untreated water, a sworn enemy of any boiler. In addition, the flash steam will overheat the water in the boiler feed tank. Most boiler feed pumps are designed to operate with condensate temperatures less than 200°. In some cases, the water could flash to steam inside the pump impeller and ruin the pump. If the condensate flashes to steam, the pump can no longer supply water to the boiler and it goes off on low water.
- Differential. When you are adjusting the setpoint, many of the controls have a differential, which is either subtractive or additive. For instance, a subtractive differential steam control set at 5 psig with a 2 psig differential would shut off at 5 psig and restart once the internal boiler pressure drops to 3 psig. If the control is an additive control, it will cycle at the differential above the setpoint. For example, if a steam boiler had an additive differential pressure control and the setpoint was 3 psig and the differential was 2 psig, the boiler would cycle between 5 and 3 psi when there is a call for heat. I prefer a wider pressure differential as it increases the boiler efficiency.
- Limit pressure control. The limit pressure control is similar to the operating control but with a couple differences. The pressure setting for the limit control is higher than the setting of the operating control. In addition, it is a manual reset control. If the steam pressure rises to the setpoint of the limit control, the control will shut off the burner and not allow operation of the burner until the steam pressure is below the setting and the manual reset button is pushed. I like to set the manual reset pressure control to about 12 psi. This is below the setting of the steam safety relief valve.
Try lowering the steam pressure on a low-pressure steam boiler for better comfort and lower heating costs.
Would you like to learn more from Ray? Check out his seminars and books.
Leave a comment
Related Posts
We always have turkey for Thanksgiving. I mean who doesn’t? My job wasn’t to cook it, though; it was to eat it.
I had written a story for Plumbing & Mechanical a while back about a fella in Canada who sent me this email: "Our problem is that five out of hundreds of univentilator co...