This all-technical, three-hour seminar will make you familiar with the many types of old steam heating systems and what goes wrong with them. Dan Holohan’s easy-to-follow...
Steam Boiler Rescue
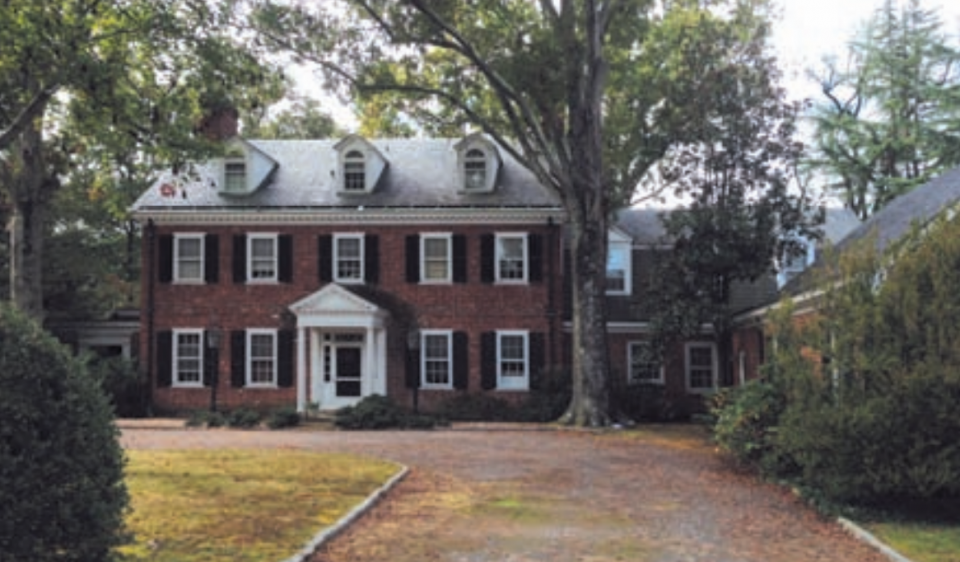
My Sunday mornings are usually spent catching up on proposals, writing, design work and other tasks that have slipped through the cracks over the previous week and can be done on my laptop at a leisurely pace. I will enjoy a cup of coffee or sugar-free Red Bull as I catch up on my work. In the background, one of the various home shows may be on the TV. Two of my favorites are “Holmes on Homes” and “Rescue My Renovation.” On these shows, a GC comes to the rescue of homeowners who have made a poor choice in a contractor and fixes all that is wrong with their home renovation in the span of a half hour episode.
I often think of those home shows as I am poking around in musty basements trying to figure out why old steam systems are not doing what they are supposed to be doing: heating my clients’ homes reliably, quietly and efficiently. Many of these systems have been badly neglected with components that are ancient and far beyond their useful life. It is a challenge to get these systems back in working order and return them to their former glory.
Many times I am asked about converting fuels, say oil to gas, or converting to hot water, as if that will magically solve the issues with a heating system. I recently attended a seminar taught by my good friend and fellow contractor, Dave Yates, on converting from steam to hot water. He presented compelling evidence and a case study that opened my eyes to this strategy. Even with this new information, I still believe that in most (but not all) situations, you are better off fixing the deficiencies in the steam system rather than converting to hot water, or forced air or heat pump, for that matter.
Rock ‘n roll boiler: Part I
Two recent jobs reinforced my opinion on this matter. The first was in the home of longtime client and punk rock legend, Ian MacKaye. Ian is well known as the front man and guitarist of Minor Threat, Fugazi and The Evens, and is the owner of Dischord Records. We have worked on the steam boiler is his residence in Washington, D.C., and we previously replaced the hot water boiler in his office at Dischord House in Arlington, Va.
Ian and I have forged a friendship over the years. We have worked on his system, a one-pipe steam system powered by a 30 year old Burnham Series 4 gas fired steam boiler. We have re-piped the header, installed main vents, replaced radiator vents, and kept his boiler functioning over the 10 years we have worked on it. We talk about business, politics, music and our shared experience growing up in the D.C. area in the late ‘70s and early ‘80s.
Ian caught the steam bug and wants to know as much as possible about his steam system. He has all of Dan Holohan’s steam books and peppers me with questions every fall when I come out for the annual service.
I issued a challenge to Ian that I could make a steam man out of him if he could teach me a few Fugazi chords on my Les Paul. After rightfully concluding that teaching me guitar was a fool’s task and a lost cause, we got to work on his steam boiler. Let’s just say that Ian is a far better steam man than I will ever hope to be on guitar.
While Ian and my lead tech, Joe Guerrero, fixed a leak on a radiator union, I vacuumed the burners, brushed out the heat exchanger sections, and flushed out the wet returns. Ian mentioned that the boiler had shut down several times last season and flooded once. I immediately suspected the #47 combination low water cutoff and feeder. When I opened the blow-off valve, boiler water the consistency of chocolate milk came out, then black coffee, then tea, until finally it ran clear. When I tried to close the blow-off valve, it would not close all the way, allowing a steady drip.
Ian asked if I could replace the valve. I had a replacement valve, but based on the age of the device I recommended replacing the entire #47 feeder/low water cutoff. I sent Joe back to the shop to retrieve one while Ian and I went to survey one of my job sites in Bethesda.
We met back at the house and tore out the old #47. Just for grins, I broke apart the housing to check the condition of the float assembly and housing. The photo above shows the results. It was completely caked with mud and sediment and long overdue for replacement. We piped in the replacement #47, replaced a cracked gauge glass, cleaned and skimmed the water line, and put the old beast back into service. At 30 plus years old, the Burnham has earned its retirement but will faithfully perform its duty for at least one more year. Another steam boiler rescue!
Country boiler: Part II
I was called to look at an old steam system in a country estate home located near Middleburg, Va. The manor house was built in 1929 and was heated by steam. A garage wing as well as a guest house wing is heated by the same steam boiler. The original coal boiler had long been replaced by the current oil fired boiler.
The current system was burning almost $3,000 worth of oil per month, and was performing poorly with water hammer, unbalanced heat, short cycling lock-outs and poor reliability. The client had retained a mechanical engineer to design the replacement system and supervise the project. We had done multiple projects for this engineer previously and he trusted our work and recommended us, even though we were the high bidder.
There was discussion of converting the system to hot water, but I did not consider this a viable alternative. The house was built in 1929 and did not have insulation in the walls and minimal attic insulation. In addition, the built-in two-pipe convectors had orifice plates instead of traps. These orifice plates would not allow sufficient flow of hot water without creating a velocity noise that would be objectionable. Along the way, someone with good intentions tried to alleviate a problem by installing motorized valves and splitting the system into four zones.
While fixing one problem, they created a bigger problem by adding the zone valves. The steam boiler can only fire at one rate. It is either off or on. When just one or two zones are calling, the boiler produces steam at a greater rate than the system can distribute it causing short-cycling on pressure. In addition, the zone valves were not dripped causing horrendous water hammer whenever a valve opened. In an attempt to minimize the short cycling, a previous service company down fired the burner from 4.5 gph to 2.5 gph. This helped the short cycling but caused a bigger problem. On design days, all of the zone valves would open, the burner would fire all day long but the boiler would just simmer, barely producing a head of steam. No wonder they were on a first name basis with their fuel oil delivery man. With steam, if you can’t see the whole system in your mind, it is very easy to keep digging a deeper hole as you attempt to fix problems.
In addition, we found undersized main vents, uninsulated steam mains and an inefficient method of DHW production. An old riveted copper storage tank, original to the house, still stored hot water while the boiler maintained a constant 180°F year round. While this produced plenty of hot water, it was extremely inefficient.
After the asbestos was remediated, we got to work with our solution. My lead tech, Brian Golden along with his crew of Fred Johnson and Chris Delmar rolled up their sleeves and got to work. The boiler was replaced with a Burnham V-904 that was sized to the connected radiator load. We stayed with oil, firing the boiler with a Beckett CF800 burner. We closed off an open window that provided combustion air and installed a motorized combustion air damper that closed during the off cycle.
The motorized valves were removed from the system. We achieved system balance through the proper sizing and location of main vents. The guest house remained a challenge as it was totally isolated from the main house and only connected to the boiler room through an underground utility tunnel. We decided to heat this zone with hot water through a shell and tube heat exchanger. The heat exchanger was connected to the boiler below the water line and a bronze three-piece Taco pump generated flow through the shell side of the heat exchanger, minimizing the chance of fouling.
The orifice plates were removed from the convectors in the guest house. Pressure held after repairing one leak. This zone does not affect the steam side of the system as it uses the pick-up factor for the approximately 35,000 BTU/hour required to heat this space.
DHW is produced through a pair of copper tankless coils connected to a 119 gallon storage tank. The boiler only fires when there is a demand for domestic hot water. It does not stay hot all of the time. Diagram 1 shows the piping detail.
The header and mains were insulated with 2-inch fiberglass pipe insulation. The accessible run-outs and returns were insulated with 1-inch fiberglass pipe insulation. The header also was wrapped with a dipped canvas pipe wrap that dries to a hard cast-like covering. The existing wet return was completely clogged with mud and sediment. Rather than try to flush it out, we replaced it with new schedule 40 black steel pipe. Since the basement was open, this was not too difficult.
After flushing, cleaning and skimming, the system was put into service in October. All the radiators in the main house were hot and the guest house was cozy warm. I’ll be back in winter to check in with the client and monitor oil consumption. I’ll be disappointed if we don’t cut fuel usage in half. Steam system rescue No. 2 complete!
Dan Foley is president and owner of Foley Mechanical, Inc. based in Lorton, Virginia. (www.foleymechanical.com). FMI specializes in radiant, hydronic and steam systems as well as mechanical systems for large custom homes.
Leave a comment
Related Posts
We always have turkey for Thanksgiving. I mean who doesn’t? My job wasn’t to cook it, though; it was to eat it.
I had written a story for Plumbing & Mechanical a while back about a fella in Canada who sent me this email: "Our problem is that five out of hundreds of univentilator co...