In this presentation, Gary Klein shares important information about air source heat pump water heaters (HPWH), with particular attention paid to where the warm air comes ...
The Return Pipe That Was a Supply
The heating business has a way of humbling you. After more than 25 years of running service calls on all types of heating and cooling systems, I had managed to tackle the toughest service problems. I began to think I knew a thing or two about these systems. Every fall, I help my crew out with trouble calls. I always seem to run into one that makes me realize I still have much to learn. What I have learned is that getting complacent and jumping to conclusions will generate call-backs.
A couple of years ago, a client called with a problem job. A well-intentioned contractor had installed a tankless water heater to provide both space heat and DHW. While he at least isolated the DHW from the space heat with a heat exchanger, this misapplied product did not work to the client’s expectations and suffered numerous breakdowns.
The client accepted my recommendation, and we installed a Triangle Tube Excellence condensing gas boiler with an integral DHW tank. This system was installed in a 1920s vintage D.C. row house with an English basement apartment. Space was tight in this basement apartment; the Excellence was chosen as it fit in the tight mechanical closet right off the kitchen (See Photo 1).
The system worked well the first winter; there were no complaints or service problems. This fall, going into the second winter, the client called to complain that the main floor and second floor radiators were hot and that the space temperature was overshooting the setpoint. The basement is on a separate zone, independent of the top two floors.
I arrived and checked the main floor thermostat. The radiators were warm, the thermostat was set to 70º, and the actual temperature was 72º. Old gravity conversion systems with cast iron radiators can store a lot of energy. A couple-degree overshoot did not seem too excessive. I was hoping that this was the reason for the complaint. Hope is typically not a good troubleshooting strategy – for good reason; this turned out not to be the cause.
I went to the basement and noticed it was very warm. The thermostat was set to 75º; the temperature was, in fact, 75º. The radiators were still hot from the last cycle, but the boiler was off and both zone valves were closed. I checked out the main floor thermostat and the Taco ZVC zone valve control and both checked out. I also checked both zone valves.
Everything checked OK, and I was scratching my head. The only thing I could surmise was that the zone valve was not closing all the way or that a bit of grit or solder was stuck on the valve seat, not allowing it to close all the way. I replaced both zone valves, proclaimed the system “fixed” and went on my way.
The next morning the irritated client called to let me know that not only was it not fixed but it was worse than ever. It was one of the first cold nights with temperatures down in the 20s, so I knew that the boiler ran most of the night. Call-backs are the worst, because you cannot put them off for a day or two. You were just there and the problem still exists: You have to go there immediately.
I cleared my schedule and sat in D.C. rush hour traffic all the way up 395 to arrive at the house and meet the client, who had taken off work twice now to let me in. This time the main floor was 74º with the thermostat set at 70º. The radiators were very warm but not hot. Again, the basement was a sauna, with the thermostat set to 75º, and the radiators very hot to the touch.
The basement zone was calling, and the zone valve was open. The main floor zone was off: I confirmed that the zone valve was closed and that the piping directly downstream of the zone valve was cool. The valve was definitely not allowing flow when it was off. I was at a loss as to what was causing the phantom flow through the main floor radiators.
What was causing this problem? This system had been in operation for over a year with no problems. What caused this problem to suddenly occur? I decided to slow down, analyze the situation and ask some questions.
What changed? After talking to the client, I got one clue. The basement apartment was not rented last winter, so the thermostat was set to 60º. It was only this fall that the apartment was rented, and the new tenant liked to keep it hot.
Another clue: Some of the piping was exposed in the basement. This was an old gravity system conversion, and the big 2-inch steel mains were accessible below some of the basement ceiling. The basement radiators were added later and piped with 3/4-inch copper. The main floor zone piping was cool at the boiler, yet the mains were very warm 10 feet away. This defied logic. What was going on?
I traced out and marked all of the piping. As I was marking the returns from the main floor, I noticed that they were very hot. How could this be? I tracked the supply and return from a basement radiator. These were smoking hot, as this zone was still calling. The basement return teed into the returns from the main floor as indicated in Figure 1 and Photo 2. This tee was about 12 feet from the boiler.
When the flow reached this tee, it backfed through the tee and up through the main floor radiators. As these were piped with 2-inch black steel, there was very little resistance to flow. The tee tying the two supply mains together acted as a crossover, feeding the remaining radiators. Mystery solved. While this backflow was not much, it was enough to warm the radiators and overheat the space. We went back and cut in two check valves, eliminating the backflow and solving the problem. This backflow through the return main had existed since we installed the boiler but was only evident when the basement tenant cranked up the heat.
It always pays to slow down and think logically rather than grasping at problems or guessing at the cause. The clues are there and the causes are evident if you take the time to analyze the facts. I didn’t on my first trip, and it cost me a call-back and an irritated client.
Dan Foley is president and owner of Foley Mechanical, Inc. based in Lorton, Virginia. (www.foleymechanical.com). FMI specializes in radiant, hydronic and steam systems as well as mechanical systems for large custom homes.
Leave a comment
Related Posts
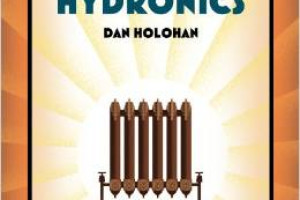
In this all-technical three-hour seminar, Dan Holohan will give you a Liberal Arts education in those Classic Hydronics systems. He’ll have you seeing inside the pipes as...
We always have turkey for Thanksgiving. I mean who doesn’t? My job wasn’t to cook it, though; it was to eat it.