In this presentation, Gary Klein shares important information about air source heat pump water heaters (HPWH), with particular attention paid to where the warm air comes ...
Water Quality with High-Efficiency Boilers
The majority of the hydronic boilers we install today are low-mass, modulating condensing boilers. Sure, we still install a few atmospheric cast iron boilers on occasion, when budget, venting or condensate drainage issues dictate this choice. But eight out of ten hot water boilers we install are high-efficiency condensing boilers. With high-mass, cast iron hot water boilers, I never really gave any thought to the quality or treatment of the system fill water. I would drain the system, cut the old boiler loose, connect the new boiler, fill and purge, and be on my way. I don’t recall ever having an issue with leaks, heat exchanger corrosion or system water quality. The heavy cast iron sections were very forgiving when it came to bad system fill water. The cast iron sections had plenty of surface area for dissolved oxygen in the water to attach to.
Contrast that with modern, low-mass condensing boilers with stainless steel water-tube or fire-tube heat exchangers. These heat exchangers have narrow passageways compared to their cast iron predecessors, with only a thin, stainless steel sheet separating the system water from the burner flame. There is very little iron in these systems for free oxygen to attach to.What little steel or iron there is in the system, such as pump volutes and expansion tanks, can quickly corrode. Here water quality is paramount, as I have learned over the years.
I installed my first condensing boiler, a Glow Core, back in the early 1990s. Condensing boilers have been my primary boiler for close to 20 years. We are now going back and replacing the first generation of condensing boilers we installed 15 plus years ago.
I recently got a call to look at one of the first modulating condensing boilers that I installed 16 years ago. We had been to this job several times over the past year for flame failure lockouts. The flame sensor would always be fouled or corroded. We would either clean or replace the sensor and all would be well for about six or eight weeks, then there would be flame lockout again. The combustion was dialed in, and flue gas recirculation was eliminated as a cause. We had very few service issues with this boiler since it was installed. Now, it seemed like we were out every two months for no heat or no DHW calls.
After pulling the burner, my lead tech, Mark Wilson, quickly determined the cause. There was a tiny pinhole in the stainless steel heat exchanger. The leaking water would turn to steam when the burner fired, causing the flame sensor to corrode and foul. In the off cycle, the tiny amount of water leaking would trickle down the condensate drain unnoticed.
When we installed this boiler, no thought was given to system water. In servicing this system over the years, no treatment chemicals were ever injected into the system. This boiler is connected to radiant floor heat, four hot deck coils, a DHW tank and a pool heat exchanger. The primary and secondary piping in this system is copper pipe. There is very little steel or iron in this system. Over time, the system water became corrosive, causing the heat exchanger to fail. I do not fault the boiler manufacturer for this heat exchanger failure. Poor water quality was the cause.
Water treatment is especially important when matching a new condensing boiler to old gravity systems with massive cast iron radiators and large steel mains. Iron oxide, sludge, sediment and other dissolved contaminants in the system water come out of solution at the hottest part of the system: the heat exchanger. These contaminants foul the heat exchanger, causing premature failure. Believe it or not, this heat exchanger failed within eight weeks of installation. While this is an extreme case, it goes to show what is going on inside the system.
We now take steps to avoid this type of heat exchanger failure. If time allows, we will inject a system cleaner such as Rhomar Hydro-Solv 9100 or Fernox F3 a week or two before the boiler is replaced. This allows the cleaner a chance to circulate and do its job before the system is drained. This cleaner is an industrial, non-foaming soap that loosens sludge and debris from the system, allowing it to be flushed and drained.
After the new boiler has been installed, filled and purged, we will then inject a system treatment such as Rhomar Pro-Tek 922 or Fernox F1. This treatment passivates the metal in the system and protects against scale and corrosion. Both the cleaner and treatment are easily installed using a small pony pump and short hoses. Both Rhomar and Fernox recently came out with small pressurized cans making the process even easier with no additional tools or hoses required.
We recently started using in-line filters on our projects to continually filter the system water and remove contaminants. We have used filters made by Fernox and Sorbox on our projects. Caleffi makes a nice one as well. These filters are reasonably priced and cheap insurance against early failure.
Steve Wieland is the east coast regional manager for NTI Boilers. NTI is a leading manufacturer of low mass high efficiency condensing gas boilers. Steve has this to say about boiler system water quality: “I always thought the need for cleaning and treating boiler water was an urban myth, until it started happening in my territory. The need for good water, proper cleaning and flushing, boiler water treatment and proper flow is an absolute must on all condensing boilers, regardless of brand, material or application. Any manufacturer who tells you otherwise is lying to you.”
Yes, this additional step causes additional time and cost to a job, but this is a marginal cost compared to premature boiler and component failure. You would never drive your work truck without changing the oil on a regular basis. Don’t install a new boiler without properly cleaning and treating the system water. Your boiler will love you for it.
Dan Foley is president and owner of Foley Mechanical, Inc. based in Lorton, Virginia. (www.foleymechanical.com). FMI specializes in radiant, hydronic and steam systems as well as mechanical systems for large custom homes.
Leave a comment
Related Posts
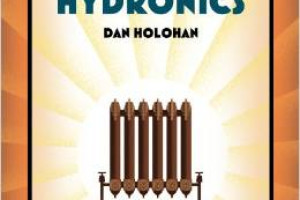
In this all-technical three-hour seminar, Dan Holohan will give you a Liberal Arts education in those Classic Hydronics systems. He’ll have you seeing inside the pipes as...
We always have turkey for Thanksgiving. I mean who doesn’t? My job wasn’t to cook it, though; it was to eat it.