In this presentation, Gary Klein shares important information about air source heat pump water heaters (HPWH), with particular attention paid to where the warm air comes ...
Why Your Boiler Needs a Low-Water Cutoff
A friend of mine who happens to be a contractor went out to look at a hot water boiler that was causing its owner a problem a few years back. It seems the flame had chewed through the back of this steel boiler and was licking up the side of the jacket.
There was no water in that boiler and yet the burner just kept running because there was nothing on that boiler that could shut it off. That boiler didn’t have a low-water cutoff. No one thought a low-water cutoff was needed because the system had an automatic water feeder. They figured that if the system developed a leak, the feeder would feed and that would be that.
The trouble was this was an old radiant heating system. The pipes were made of metal and some of them had sprung leaks. The original installer hadn’t thought to use a vapor barrier below the concrete slab, so when the pipes leaked, the water went down, not up, and no one noticed it.
So the feed valve did what it was supposed to do. It fed a lot of water into the system in a hopeless attempt to bring the system pressure back up to 12 psi. That feeder didn’t have a prayer, though, because the pipes were leaking as fast as the feeder was feeding. And did I mention that this job was in a part of the country where the water was as hard as an anvil?
Now, here’s the thing about hard water. Calcium and magnesium, which are the elements in water that give it its "hardness," have this weird property of being inversely soluble. That means that when the boiler heats the water, these elements come out of solution and turn into a rock-hard solid. In other words, calcium and magnesium do the opposite of what sugar and salt do when they hit hot water. Calcium and magnesium form what we commonly call "lime." It’s the stuff you find in the bottom of a water heater after a few years.
On this particular job, however, the calcium and magnesium kept building up inside the guy’s boiler and that became a problem for him. Before anyone noticed, the lime had sealed the insides of the boiler. Less and less water flowed into the boiler; it was all going out to the pipes buried beneath the concrete floor. The thermostat kept calling for heat and the circulator kept spinning in space, but the boiler was dry. The automatic water feeder kept trying to keep up with the loss in pressure. And the burner kept running. And after a while, that burner chewed through the steel sides of that boiler and nearly burned down the building.
When my friend installed the new boiler, he put a low-water cutoff on it. He didn’t ask the people if they wanted one; he just did it. Wouldn’t you have done the same?
I once looked at a job here on Long Island. It was a brand-new, four-section cast iron boiler. It was attached to a simple, one-zone Monoflo loop. There was one circulator on the return side of the system, and one flow-control valve on the supply. The boiler had a tankless coil for domestic hot water. The boiler also had an internal leak from a sand hole, which the folks at the foundry had missed.
This boiler ran, but it was losing water up the chimney. The rate of loss was such that the system pressure never got low enough to cause the automatic feeder to feed. The steam that was forming inside the boiler kept the pressure up. But the pressure never went high enough to pop the relief valve either. To make things worse, the temperature the aquastat was seeing was not accurate because the aquastat’s probe was in a well, and no one put heat transfer grease into that well, so the burner kept running. It was a very bizarre hydraulic balancing act, but what you need to know is that the water left the boiler, but not the system. The pressure inside the boiler pushed with equal force against the supply and return mains. The boiler was filled with nothing but fire and red-hot iron and the water was all out in the system piping.
And then the lady of the house told the man of the house that she was chilly, and she asked him to turn up the thermostat. Which he did. And when the water in the pipes hit that hot metal, the water exploded into steam, causing the back section of the boiler to rupture with obscene violence. That back section became the engine that drove the other three cast-iron boiler sections across the basement. It ripped itself away from the piping and nearly knocked the house off its foundation.
The new boiler, needless to say, had a low-water cutoff because an automatic water feeder can’t possibly protect anyone against this sort of thing. The homeowners now understood this. The contractor didn’t have to ask them if they wanted one; he just included it in his price. It’s pretty easy to do that on the heels of a disaster. And you know what? The contractors involved in those two jobs now install low-water cutoffs on every stinking boiler they install. As should every contractor.
Leave a comment
Related Posts
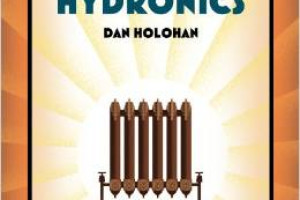
In this all-technical three-hour seminar, Dan Holohan will give you a Liberal Arts education in those Classic Hydronics systems. He’ll have you seeing inside the pipes as...
We always have turkey for Thanksgiving. I mean who doesn’t? My job wasn’t to cook it, though; it was to eat it.